Specialist Tips for Picking the Right Metal Stamping Providers for Your Demands
Specialist Tips for Picking the Right Metal Stamping Providers for Your Demands
Blog Article
Advanced Techniques in Steel Stamping for Precision Manufacturing
As industries continuously require better tolerances and elaborate styles in their steel components, the quest for advanced strategies in metal marking has actually increased. From the application of innovative multi-stage marking procedures to the integration of advanced automation modern technologies, the landscape of metal stamping is going through an extensive change.
Advanced Multi-Stage Stamping Procedures
Reviewing the intricacies of sophisticated multi-stage stamping processes exposes the advanced methods utilized in contemporary production methods. Metal Stamping. Multi-stage marking is a complicated process that includes several steps to transform a flat sheet of metal into a final stamped product. Making use of progressive dies, where different operations are performed at each phase of the stamping process, permits for high precision and effectiveness in the manufacturing of intricate steel parts
Throughout the first phases of multi-stage marking, the flat metal sheet is fed right into the stamping press, where a collection of passes away are used to reduce and form the material. Subsequent stages entail added creating, flexing, and punching operations to further improve the part. Each stage is meticulously made to construct upon the previous one, leading to the production of intricate geometries with limited tolerances.
Advanced multi-stage stamping procedures need a high level of experience and accuracy to make sure the quality and consistency of the stamped components. By using sophisticated equipment and tooling, makers can create a vast array of steel elements with efficiency and precision.
Accuracy Tooling Innovations
Accuracy tooling developments have reinvented the steel stamping sector, enhancing efficiency and top quality in making procedures. CNC systems allow for intricate designs to be translated directly into tooling, ensuring accuracy and repeatability in the stamping procedure.
Additionally, the combination of sensing units and real-time surveillance capacities in precision tooling has enabled makers to find and resolve problems promptly, reducing downtime and decreasing scrap rates. By incorporating wise innovation into tooling, operators can optimize specifications such as stress, speed, and positioning during the stamping procedure, causing boosted item high quality and enhanced efficiency.
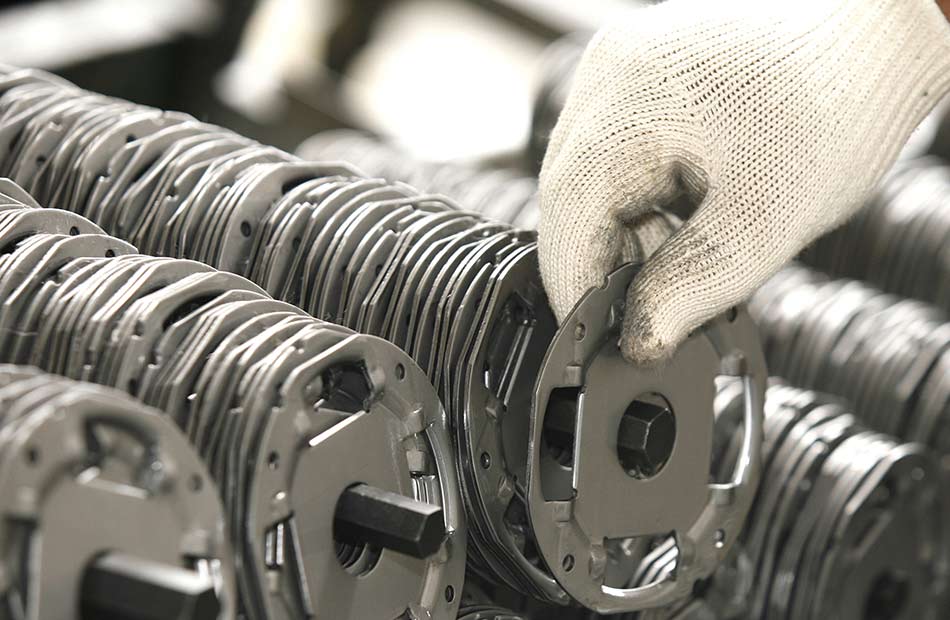
Automation in Steel Stamping
The advancement of accuracy tooling technologies in the steel marking market has led the way for considerable improvements in automation, transforming the manufacturing landscape towards boosted effectiveness and performance. Metal Stamping. Automation in metal marking entails using advanced equipment and robotics to perform different jobs generally accomplished by human operators. This shift in the direction of automation supplies numerous benefits, including boosted accuracy, much faster manufacturing cycles, and reduced labor costs
One key element of automation in steel stamping is the application of computer numerical control (CNC) systems, which allow specific control over the marking process. CNC modern technology enables for the creation of complicated and elaborate metal components with regular quality. Furthermore, automated systems can be programmed to run continuously, bring about higher output prices and shorter preparations.
Additionally, automation boosts office safety by lowering hands-on handling of hefty materials and decreasing the danger of crashes (Metal Stamping). As manufacturing markets proceed to embrace automation, the future of metal stamping holds wonderful guarantee for also greater effectiveness and advancement
High-Speed Stamping Techniques

One of the primary benefits of high-speed stamping methods is the capacity to produce a huge volume of parts in a much shorter quantity of time compared to standard stamping approaches. This enhanced productivity not only permits suppliers to satisfy limited production due dates but also makes it possible for expense savings through economic situations of range. Furthermore, high-speed stamping can aid minimize material waste by optimizing the material use during the marking process.
Additionally, high-speed marking techniques find out here now often incorporate innovative attributes such as fast die adjustment systems and real-time monitoring abilities, better enhancing the general effectiveness and adaptability of the metal marking process. As technology remains to development, high-speed marking is expected to play an essential role in driving the future of precision manufacturing.
Quality Assurance in Stamping Workflow
Reliable quality assurance steps are have a peek here essential for ensuring the reliability and uniformity of metal marking procedures. Quality assurance in marking operations involves a collection of systematic procedures focused on identifying and stopping problems in the made parts. One critical element of quality assurance in steel marking is the use of sophisticated evaluation methods such as optical inspection systems and coordinate measuring machines (CMMs) to validate the measurements and resistances of stamped parts.
Furthermore, quality assurance procedures in marking procedures commonly consist of the application of analytical process control (SPC) techniques to monitor the manufacturing procedure in real-time and make sure that it remains within acceptable restrictions. By analyzing data and determining patterns, manufacturers can proactively resolve any variances from the wanted quality requirements.
In addition, top quality control in metal marking operations also useful link entails extensive product screening to make sure that the raw products utilized satisfy the called for specifications for the stamping process. This may include conducting product hardness tests, tensile stamina tests, and dimensional examinations to ensure the quality and honesty of the stamped elements. Generally, executing robust quality assurance procedures is crucial for accomplishing top notch stamped parts constantly.
Conclusion
To conclude, progressed methods in steel marking play a critical role in accuracy production processes. Via multi-stage stamping processes, cutting-edge tooling services, automation, high-speed methods, and strenuous quality assurance procedures, manufacturers can achieve greater levels of accuracy and efficiency in their operations. These improvements in steel marking technology have actually allowed companies to create complicated components with limited tolerances, eventually resulting in enhanced product high quality and client satisfaction in the manufacturing industry.
Report this page